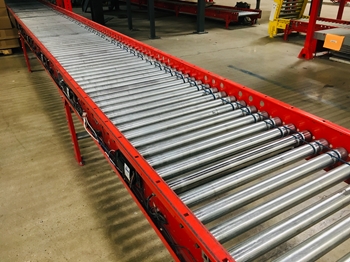
Companies that often depend on their conveyor system for their daily operations do not always take proper care of them, so when a breakdown occurs the company can be out of commission for a long time. It usually causes production to come to a screeching halt, resulting in idle employees, late shipments, and overall unsatisfied customers. Some of the common mistakes you can avoid are as follows:
Be observant: It might seem silly but watching and listening to your conveyor system can help determine inefficiencies. Hearing squeaking or rubbing is a sign that the system is not functioning properly and seeing a dust buildup below a belted conveyor could be a sign of excessive wear. Looking for signs like this and listening to your equipment from time to time can save you in repair costs down the road. Waiting for something to go wrong and only acting at that point will result in expensive repairs and long delays.
Another piece of the conveyor to pay attention to is the temperature of motors and reducers because drastic temperature changes are a sign of the system being overloaded. This could mean too much weight on the conveyor’s belt or rollers, or an inappropriate type of conveyor was being applied to perform a specific function.
Keep proper and regular maintenance records: Making sure that proper maintenance logs are being kept on a regular basis will ensure your conveyor system lasts as long as possible. Just like getting maintenance checks and oil changes help extend the useful life of a vehicle, an up-to-date log will do the same thing for a conveyor. If multiple shifts of workers use the same equipment, the logs must stay up to date to ensure accuracy. If your conveyor ever fails to work when in regular use, your up-to-date maintenance records will help your case when you approach the manufacturer.